Following the signing of a MoU wherein the Coonoor Municipality would be responsible for the collection and transport of the waste and Clean Coonoor for its disposal, both the organisation and the local body faced an uphill task as this hill town is plagued with hurdles such as topography, lack of adequate workforce, high transportation costs, and near absence of suitable markets for disposal of recyclables.
Through trail and error the efforts succeeded, and after a period of 4 years, a comprehensive waste management programme is now in place.
Leaving an indelible mark on the landscape of tomorrow.
The Time Line of Events
- Legacy Waste removed and landscaping done
- 2 TPD Resource Recovery Centre established and made functional from Oct 2019
- Handling Capacity of the Resource Recovery Centre increased to 5 TPD by the end of 2020
- 4 TPD Composting Unit established and made functional since Dec 2021
- Composting Unit upgraded to handle 8 TPD from March 2022
- All recyclable waste collected and transported to their respective facilities – non-recyclables disposed as per Pollution Control Board Norms
- The undertaking has presently evolved as a technically sustainable model which can take in 7 TPD of Dry & 10 TPD of Wet, and furthermore can be emulated in similar settings elsewhere in this district and in other hill towns.
The Resource Recovery Centre
Dry Waste collected here is re-sorted into recyclables and non recyclables, and dealt with accordingly. Designated Recyclables are either despatched to aggregators or recyclers, or to waste to energy plants, whereas non-recyclables are dealt within the premises as per Pollution Control Board Norms.
The Resource Recovery Centre is run along the lines of a Mixed-waste processing facility (MWPF) / Dirty Materials Recovery Facility, which takes in a waste stream of both recyclables and non-recyclables and then proceeds to separate out designated recyclable materials through a combination of manual and mechanical sorting.
The designation of recyclables, for those of low value in particular, is entirely dependent on the methodology of re-sorting that is adopted, which is in turn dictated by prevailing market forces, availability of Extended Producer Responsibility (EPR), and such.
Whenever EPR is available to recoup expenses incurred in transportation which entails considerable distance – a methodology which involves production of a Combustable Fraction out of zero-value plastics, textile waste, soiled paper, and other similar material, which are baled together and the despatched to cement kilns and Waste to Energy (WtE) Plants for use as an Alternate Fuel Resource (AFR).
In the absence of EPR, zero-value plastics alone are baled and despatched to either cement kilns and WtE Plants as AFR, or when circumstances permit for pyrolysis a much more eco-friendly process with a much lower carbon footprint. All other combustable material are disposed off through onsite High-Temperature Closed Burning.
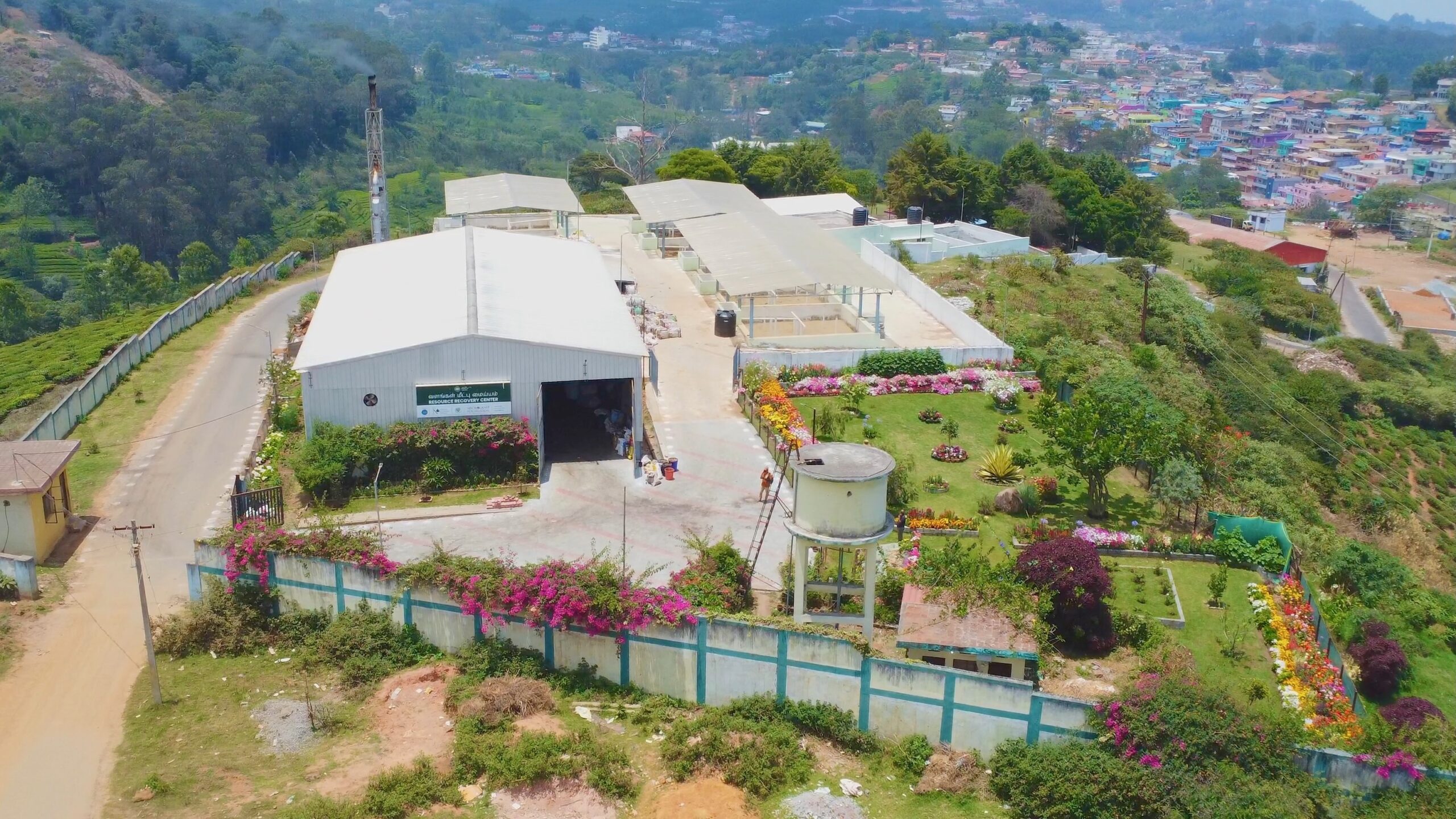
The Wet Waste Processing Unit
Butcher Residue, Fibrous Waste and Kitchen Leftovers are mixed in a ratio of 1:1:5-6 and then pulverised prior being heaped in windrows for composting. Once mature the composted material is sieved, bagged and sold chiefly to floriculturists and horticulturists at a nominal price.
In-Shelter Windrow composting has been chosen over other options on account of its flexibility. Unlike other methods which have a handling range and an upper limit, windrows can take in volumes both large and small, a feature common when it comes to dealing with municipal waste. Furthermore it is also more adaptable to the vagaries in climatic conditions, as the height of the windrow can be easily manipulated according to the prevailing temperatures and humidity. It may also be argued that other methods generate a much lower carbon footprint, but this can be offset to a certain extent by frequent monitoring of the core temperature and moisture content of the individual windrows and turning them accordingly.
The compost conversion rate hovers around 10-15% and is dependent on the character and moisture content of the feedstock and the quantum of bulking agents added. Common bulking agents used are locally available wood-ash, garden waste such as leaf litter, and dried prunings, clippings and trimmings.
Under favourable conditions the compost is usually ready by 40 days after which it is subjected to a sun drying process. It is finally batch tested for both fertility and absence of heavy metals as per the guidelines issued in the Fertiliser Control Order (FCO) 1985, before being issued or sold for use.
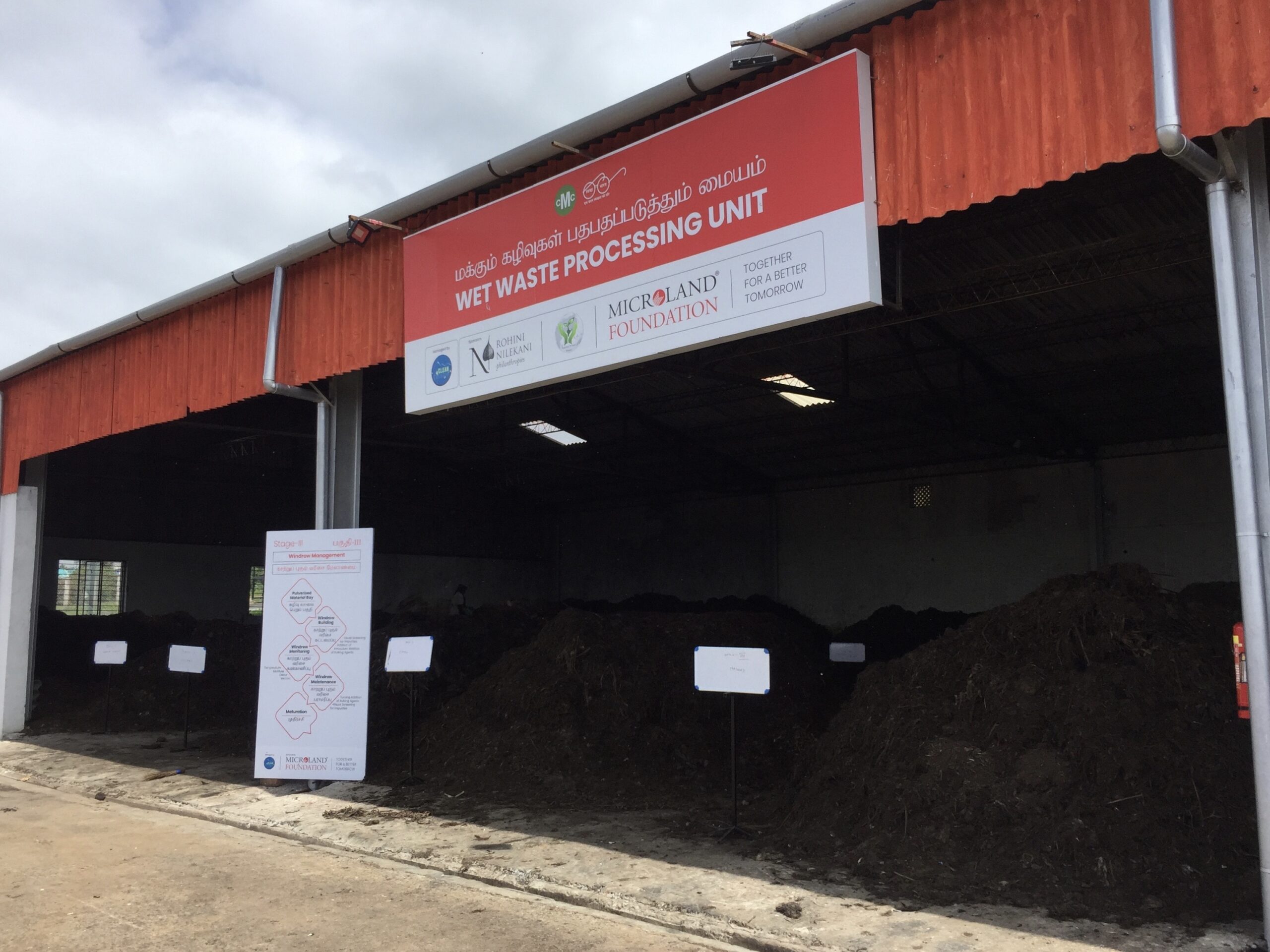
FAQs
Are all types of plastic waste recyclable?
Yes, in one form or the other, while most types can be handled by primary or secondary recycling methods, the bulk can be dealt only either by tertiary methods whereby the plastic is broken down to extract oil, or through quaternary recycling which involves co-processing plastic waste as fuel.
But recycling is not an end by itself, focus should be on the 4 ‘Rs’ which have a much lower carbon footprint – ‘Refuse – Reduce – Reuse – Repurpose.’
What is mismanaged plastic waste?
Mismanaged plastic waste is waste that is not recycled, incinerated, or kept in sealed landfills. It includes materials burned in open pits, dumped into seas or open waters, ordisposed of in unsanitary landfills and dumpsites.
What are the consequences of mismanaged plastic waste
Unlike other materials, plastic does not biodegrade. It can take up to 1,000 years to break down, so when it is discarded, it builds up in the environment until it reaches a crisis point. This pollution chokes marine wildlife, damages soil and poisons groundwater, and can cause serious health impacts.
How can I help?
While the plastic pollution crisis needs systemic reform, individual choices do make a difference. Such as shifting behaviour to avoid single-use plastic products whenever possible. If plastic products are unavoidable, they should be reused or repurposed until they can no longer be used – at which point they should be recycled or disposed of properly. Bring bags to the grocery store, and if possible, striving to purchase locally sourced and seasonal food options that require less plastic packaging and transport.